17.11.2022
Valorization of lignin in polymer composites
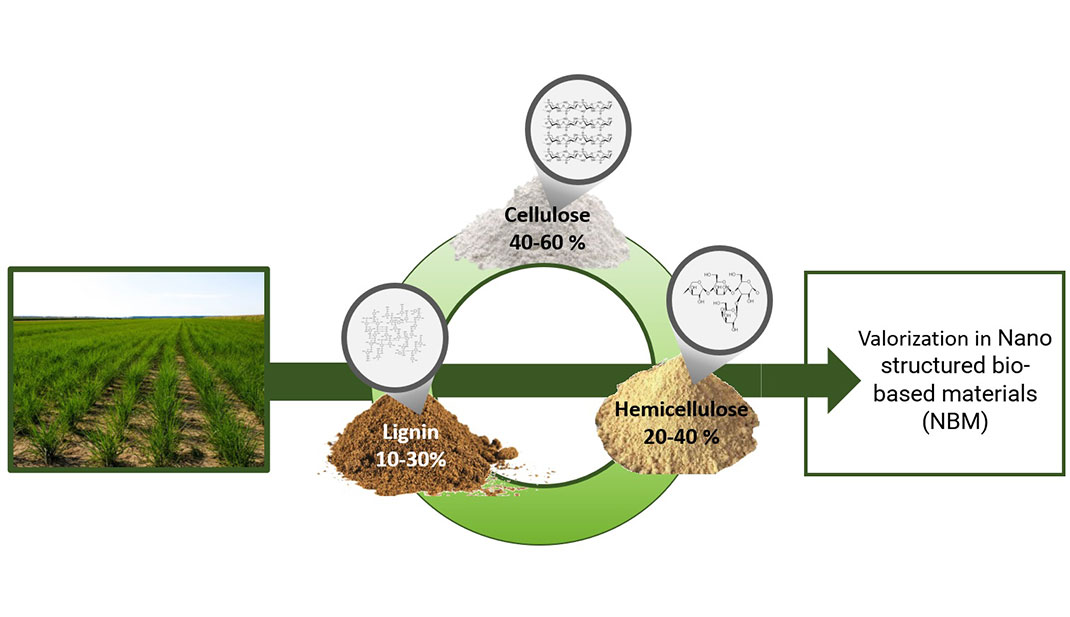
Lignin is the most abundant aromatic biopolymer and the second most abundant polymer on the planet, and it has been estimated that more than 300 billion tons of lignin is present in the Earth with an enormous yearly biosynthesis of ~20 billion tons [1].
Where does all this lignin come from?
Lignin is produced in large quantities as a by-product in the pulping and cellulosic ethanol industries. It is one of the three main components of lignocellulose, with a content of ca. 10-25 % depending on the nature of biomass, with the other two being cellulose (30-50 %) and hemicellulose (15-35%) [2]. Most of this lignin is combusted to generate electricity.
The properties of lignin
Lignin is effective as an antioxidant and for UV protection due to its radical scavenging ability. It does however posses some disadvantages that can be managed with advanced fractionation and processing techniques.
Advantages and disadvantages of lignin
What to do with all this lignin?
Economic analysis has proven that it is not economically appealing, especially in the long-term, to use lignin only for energy, compared with applying lignin for high-value chemicals and materials. For instance, when used as energy or as a solid fuel to replace natural gas, lignin is worth only about 150 € per ton [3]. Valorizing lignin into aromatics and polymers, valued over 1000–1200 € per ton, could greatly improve the economics of lignin applications. Lignin's potential market has been estimated to be as large as 242 billion €.
Lignin in polymer composites
An integral part of the establishment of a bioeconomy in Europe is the development of biobased plastics, i.e., plastics made from renewable sources, as it will contribute towards the gradual independence of our society from finite and non-renewable fossil sources. Lignocellulosic biomass is an abundant source of high added value chemicals. The utilization of lignin is a topic of intense research in the last decade [4], and one of the simplest approaches is its use as a filler in polymer composites [5–8]. Lignin can reduce the cost and increase the biobased nature of polymer composites, while imparting antioxidant, antibacterial and antimicrobial properties. Therefore, it is often blended with polymers such as polyethylene, PE and polypropylene, PP to improve their thermal oxidative resistance.
Lignin vs nanolignin
When directly used for materials, lignin has much lower strength than most synthetic polymers due to its insufficiently high molecular weight, and it has poor compatibility with many synthetic polymers. :arge particle size is a responsible factor against more widespread usage of lignin as filler, since the commercial lignin shows particle sizes ranging from 10 μm to even more than 100 μm. Reducing the size of fillers is known to be beneficial for polymer composites, as larger filler surface areas can impart improved properties to the polymeric matrices. Such particles are too large and may exhibit detrimental impacts on mechanical properties of the resulting composites containing the microfiller at variable contents. The reinforcing effect of lignin for polymer matrix intensively depends on particle size and strong interfacial bonding with the matrix. For this reason, methods to reduce the particle size of lignin have been in the spotlight to make the introduction of lignin as a polymer additive easier and more beneficial [9,10].
Nanolignin can significantly alter the properties of polymers. Small quantities of nanolignin can block UV light, improve thermal and mechanical properties the hydrophobicity and the the crosslinking densities of polyurethanes, all very attractive features for insulating materials. [11] It can also have biomedical applications, as it imparted PVA with antioxidant and antimicrobial behavior with adding only 3 wt% in the composite. [12] Nanolignin can also be used as an initiator for the polymerization of lactides, a concept that is being explored within the BIOMAC project. [13]
The value chain of lignin in BIOMAC
The BIOMAC ecosystem has the capacity to cover the whole value chain of lignin, starting from biomass supply all the way to valorization in composite materials. BIOMAC offers the following services to any client operating in the field of nano-structured bio-based materials (NBM), aiming to upgrade existing or develop new concepts within the lignocellulosic value chains of nanomaterials and polymers, starting from Technical Readiness Level (TRL) 4-5.
BIOMAC can fractionate lignin with organosolv-steam explosion and hydrothermal pretreatment of biomass.
The
semi-continuous organosolv-steam explosion pre-treatment Pilot Line is capable of fractionating lignocellulosic biomass (e.g. agricultural and forest residues) to its three main polymer components, i.e. cellulose, hemicellulose and lignin. It offers unique advantages by combining the effects of steam explosion with that of hemicellulose and lignin solubilization (organosolv) in ethanol/water mixtures. The Semi-continuous PL of LTU provides the additional benefit of solid/liquid separation that can take place during operation at high temperature and pressure, simulating the continuous organosolv operation mode.
The
hydrothermal pre-reatment Pilot Line of BBEPP can obtain fractions of lignin, hemicellulose, cellulose with parameter optimization to achieve the desired monomeric characteristics while limiting the formation of unwanted by-products (inhibitors).
BIOMAC can transform lignin to new attractive materials, such as nanolignin.
To increase the added value of lignin, BIOMAC offers innovative transformation processes via its Pilot Lines:
Production of Nanolignin
The
US assisted pilot reactor for the production of nanolignin of CNANO can produce stable colloidal suspensions of lignin nanoparticles (NL) in the range of 10 to 500 nm by physical treatment via the means of ultrasonication (US), thus avoiding the need of any additional (and potentially hazardous) chemical pre‐ or post‐treatments.
The
pyrolysis and carbonization Pilot Line of UEDIN can transform lignin to biochar, which has high porosity, high thermal stability and tunable surface functionality, controllable electrical conductivity and thus is a polymer additive with great properties. Biochar is a great biobased alternative to carbon black, which has a solid industrial reputation for plenty of commodities such as tires and ink production.
BIOMAC can add lignin products in biobased polymers via reactive extrusion and 3D printing.
The
reactive extrusion (REX) for PLA and PLA copolymer based nanocomposites of AIMPLAS offers faster polymerization (from hours to a few min), the ability to work in a continuous mode, showing better mixing/dispersion capacity, and making easier to handle high viscosity materials in a free or almost free solvent process. The polymerization of PLA and its copolymers can be carried out in presence of nanolignin, thus allowing the in-situ polymerization of PLA nanocomposites to be extruded into pellets. The production capacity is 10 kg/h and the process is monitored in-line by a near-infrared sensor developed in the BIOMAC project.
The
additive manufacturing Pilot Line of AIMEN allows Large Format Additive Manufacturing of thermoplastic polymers and composites containing lignin or biochar, for creating complex geometries, with a thermal camera for monitoring.
Applications of lignin and its products in the BIOMAC project
BIOMAC will demonstrate the valorization of lignin and biochar in
agricultural applications, such as mulch films. Biochar will be used to nano-reinforce PLA and create a material with enhanced optical properties and UV/thermal resistance.
Nanolignin will also be used in PLA-based foils for
food packaging applications. It will offer antioxidant, antimicrobial and antifungal properties. In
construction applications, biochar will be inlcuded in 3D printed thermoplastic polyurethanes. Finally, the electrical conductivity of biochar will be taken advantage of for
sustainable printed electronics production.
To learn more about the services offered by BIOMAC and the open call!
References
[1]
S. Sethupathy, G. Murillo Morales, L. Gao, H. Wang, B. Yang, J. Jiang, J. Sun, D. Zhu, Lignin valorization: Status, challenges and opportunities, Bioresour. Technol. 347 (2022) 126696. doi:10.1016/j.biortech.2022.126696.
[2]
M.J. John, M.C. Lefatle, B. Sithole, Lignin fractionation and conversion to bio-based functional products, Sustain. Chem. Pharm. 25 (2022) 100594. doi:10.1016/j.scp.2021.100594.
[3]
C.C. Xu, L. Dessbesell, Y. Zhang, Z. Yuan, Lignin valorization beyond energy use: has lignin’s time finally come?, Biofuels, Bioprod. Biorefining. 15 (2021) 32–36. doi:10.1002/bbb.2172.
[4]
C.G. Yoo, A.J. Ragauskas, Lignin Utilization Strategies: From Processing to Applications, American Chemical Society, 2021.
https://pubs.acs.org/doi/book/10.1021/bk-2021-1377.
[5]
M.N. Collins, M. Nechifor, F. Tanasă, M. Zănoagă, A. McLoughlin, M.A. Stróżyk, M. Culebras, C.A. Teacă, Valorization of lignin in polymer and composite systems for advanced engineering applications – A review, Int. J. Biol. Macromol. 131 (2019) 828–849. doi:10.1016/j.ijbiomac.2019.03.069.
[6]
D. Kun, B. Pukánszky, Polymer/lignin blends: Interactions, properties, applications, Eur. Polym. J. 93 (2017) 618–641. doi:10.1016/j.eurpolymj.2017.04.035.
[7]
E. Lizundia, M.H. Sipponen, L.G. Greca, M. Balakshin, B.L. Tardy, O.J. Rojas, D. Puglia, Multifunctional lignin-based nanocomposites and nanohybrids, Green Chem. 23 (2021) 6698–6760. doi:10.1039/d1gc01684a.
[8]
C. Pappa, E. Feghali, K. Vanbroekhoven, K.S. Triantafyllidis, Recent advances in epoxy resins and composites derived from lignin and related bio-oils, Curr. Opin. Green Sustain. Chem. 38 (2022) 100687. doi:10.1016/j.cogsc.2022.100687.
[9]
S. Beisl, A. Miltner, A. Friedl, Lignin from micro- to nanosize: Production methods, Int. J. Mol. Sci. 18 (2017) 1244. doi:10.3390/ijms18061244.
[10]
W. Yang, E. Fortunati, F. Dominici, J.M. Kenny, D. Puglia, Effect of processing conditions and lignin content on thermal, mechanical and degradative behavior of lignin nanoparticles/polylactic (acid) bionanocomposites prepared by melt extrusion and solvent casting, Eur. Polym. J. 71 (2015) 126–139. doi:10.1016/j.eurpolymj.2015.07.051.
[11]
G. Qi, W. Yang, D. Puglia, H. Wang, P. Xu, W. Dong, T. Zheng, P. Ma, Hydrophobic, UV resistant and dielectric polyurethane-nanolignin composites with good reprocessability, Mater. Des. 196 (2020) 109150. doi:10.1016/j.matdes.2020.109150.
[12]
W. Yang, H. Ding, G. Qi, C. Li, P. Xu, T. Zheng, X. Zhu, J.M. Kenny, D. Puglia, P. Ma, Highly transparent PVA/nanolignin composite films with excellent UV shielding, antibacterial and antioxidant performance, React. Funct. Polym. 162 (2021) 104873. doi:10.1016/j.reactfunctpolym.2021.104873.
[13]
W. Yang, L. Xiao, H. Ding, P. Xu, Y. Weng, P. Ma, Fabrication of UV- And Heat-Resistant PDLA/PLLA- g-Nanolignin Composite Films by Constructing Interfacial Stereocomplex Crystallites, ACS Sustain. Chem. Eng. 9 (2021) 15875–15883. doi:10.1021/acssuschemeng.1c05559.